
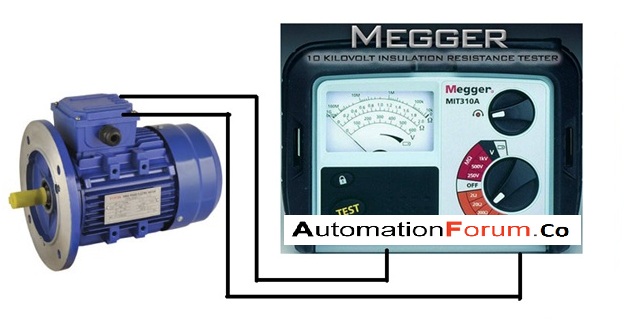
This is especially true if there is ambient moisture or the motor has been unused for a while. Fairly new bearings are prone to seizure because the tolerances are tighter. If not, there is an obstruction inside or a seized bearing. In all but the largest motors the shaft should turn freely. With power disconnected and locked out, attempt to turn the motor by hand. If the electrical supply checks out, examine the motor itself. The idea is to match supply voltages and load impedances so as to balance the three legs. If these readings vary by a few volts, it may be possible to equalize them by rolling the connections, taking care not to reverse rotation. In a three-phase hookup, all legs should have substantially equal voltage readings, with no dropped phase. When the circuit electrical load is close to the circuit capacity, the voltage drop should not exceed 3% for optimum motor efficiency.

When there is no electrical load, the same voltage should appear at both ends of the branch circuit conductors. What you’re looking for is essentially the same voltage level as measured at the entrance panel main breaker. Take readings at accessible points including disconnects, the motor controller, any fuses or junction boxes, and so on, back to the over-current device output at the entrance panel. If there is no voltage or reduced voltage, work back upstream. If the motor is completely unresponsive, no ac humming or false starts, take a voltage reading at the motor terminals. This tester is capable of providing diagnostic information for all kinds of motors. Preliminary tests generally are done using the ubiquitous multimeter. If the motor itself has developed a fault, the fault may be a burnt wire or connection, a winding failure including insulation deterioration, or a deteriorating bearing.Ī number of diagnostic tools, such as clamp-on ammeters, temperature sensors, a Megger or oscilloscope, can help illuminate the problem. Another possibility is that the driven load is jammed, binding or mismatched.

Sometimes the trouble lies within the power supply, including branch circuit conductors or a motor controller. When an electric motor fails to start, runs intermittently or hot, or continually trips its overcurrent device, there my be a variety of causes. Knowing some basic methods and techniques along with having a few test instruments handy helps detect and diagnose problems with ease. So when a motor fails to operate it may not be obvious what the problem is. Knowledge of the basics together with powerful new test equipment vastly simplifies the job.Įlectric motors have had a reputation for being a mix of science and magic. Either will be cause to discard or rebuild the motor.Testing electric motors doesn’t have to be a mystery. Compare each segment with every other segment and look for either open (infinity ohms) or shorted (zero-ohms) armature windings. Check for shorts or open armature windings by touching one test lead to one commutator (the grooved copper section that contacts the brushes) segment and the other test lead to another segment. Generally, brush length should be at least twice their width or replace them. On brush-type motors, inspect the brushes to make sure they are still serviceable. Otherwise you will have to trust that if the windings all read about the same, they are functioning correctly.
#How to check motor winding with multimeter manual
Compare the figures to the manufacturer's test specification in the service manual if one is available. Each of the sets of windings should read about the same ohms value.

Keep the multi-meter set for 30,000-ohms and touch one test lead to one terminal and the other to another terminal. Test for direct shorts in the motor's power windings in induction (non-brush type) motors.
